Standardisasi Nasional Indonesia (SNI) plays a crucial role in ensuring the quality and safety of products and services across various industries in Indonesia. As the national standardization body, SNI sets the benchmark for quality assurance, helping businesses and consumers alike make informed decisions. Whether you're a manufacturer, importer, or consumer, understanding SNI is essential for maintaining high standards in your operations or purchases. This article delves into the intricacies of SNI, its significance, and how it impacts various sectors in Indonesia.
For businesses operating in Indonesia, compliance with SNI standards is not just a recommendation but often a legal requirement. These standards cover a wide range of products, from food and beverages to electronics and construction materials. By adhering to SNI, companies can ensure their products meet national quality benchmarks, thereby enhancing consumer trust and market competitiveness. Moreover, SNI certification can open doors to new business opportunities, as it is often a prerequisite for government contracts and international trade.
Consumers, on the other hand, benefit from SNI by having access to safer and more reliable products. The SNI label assures buyers that a product has undergone rigorous testing and meets specific quality criteria. This is particularly important for items that directly impact health and safety, such as electrical appliances, food products, and automotive parts. As we explore further, we will uncover the history, implementation, and future of SNI, providing a comprehensive understanding of its role in Indonesia's economic landscape.
- The Unfiltered Truth About Anna Sawais Relationships
- The Ultimate Guide To Shubhashree Saho Bio Career And Achievements
Table of Contents
- History of SNI
- The Importance of SNI in Quality Assurance
- Understanding the SNI Certification Process
- Key Sectors Impacted by SNI
- Challenges in SNI Implementation
- SNI vs International Standards
- How SNI Protects Consumers
- Future Developments in SNI
- Benefits of SNI for Businesses
- Conclusion: The Role of SNI in Indonesia's Growth
History of SNI
The origins of Standardisasi Nasional Indonesia (SNI) date back to the early 1990s when the Indonesian government recognized the need for a unified framework to regulate product quality. Established under the auspices of the National Standardization Agency (BSN), SNI was designed to harmonize quality standards across various industries, ensuring consistency and reliability in both domestic and international markets. Over the years, SNI has evolved to encompass a wide array of sectors, adapting to technological advancements and changing consumer demands.
Initially, SNI focused on basic industrial products and agricultural goods, but its scope has since expanded significantly. Today, SNI standards cover everything from food safety and environmental protection to information technology and renewable energy. This expansion reflects Indonesia's commitment to aligning its national standards with global benchmarks, thereby enhancing its competitiveness on the international stage. The evolution of SNI has been marked by continuous collaboration with international organizations, such as the International Organization for Standardization (ISO) and the World Trade Organization (WTO).
The development of SNI has not been without challenges. Early efforts faced resistance from businesses that viewed standardization as an additional burden. However, as the benefits of SNI became evident—such as improved product quality and increased market access—more companies began to embrace these standards. The government also played a pivotal role by introducing regulations that mandated SNI compliance for certain products, further solidifying its importance in the national economy. Understanding this history provides valuable context for appreciating the current state and future potential of SNI in Indonesia.
The Importance of SNI in Quality Assurance
Quality assurance is at the heart of SNI's mission, ensuring that products and services meet stringent criteria before reaching consumers. By setting clear benchmarks for quality, SNI helps businesses maintain consistency in their offerings, which is crucial for building brand reputation and customer loyalty. For example, in the food and beverage industry, SNI standards ensure that products are free from harmful contaminants and meet nutritional labeling requirements, giving consumers peace of mind.
One of the key ways SNI contributes to quality assurance is through its certification process. Products that achieve SNI certification undergo rigorous testing and evaluation by accredited laboratories. This process verifies that the product meets all relevant standards, from material composition to performance metrics. For instance, electrical appliances must pass safety tests to prevent hazards like short circuits or overheating. This level of scrutiny ensures that consumers receive products that are not only functional but also safe to use.
Moreover, SNI plays a vital role in fostering innovation within industries. By setting high standards, SNI encourages businesses to invest in research and development to meet or exceed these benchmarks. This drive for innovation often leads to improved product designs, enhanced efficiency, and better sustainability practices. For example, in the automotive sector, SNI standards have pushed manufacturers to develop more fuel-efficient and environmentally friendly vehicles. Ultimately, SNI's focus on quality assurance benefits both businesses and consumers, creating a win-win situation for all stakeholders involved.
Key Benefits of SNI Certification
- Enhanced product quality and reliability
- Increased consumer trust and brand reputation
- Improved market access, including eligibility for government contracts
- Reduced risks of product recalls and liability issues
- Alignment with international standards for global competitiveness
Understanding the SNI Certification Process
Obtaining SNI certification is a structured and rigorous process designed to ensure that products meet the highest quality and safety standards. The process begins with an application submitted to the National Standardization Agency (BSN) or an authorized certification body. This application includes detailed product specifications, manufacturing processes, and quality control measures. Once the application is reviewed and deemed complete, the product undergoes a series of evaluations and tests conducted by accredited laboratories.
The testing phase is critical, as it verifies whether the product complies with the relevant SNI standards. For example, if the product is a household appliance, it will be tested for electrical safety, energy efficiency, and durability. These tests are conducted using state-of-the-art equipment and methodologies to ensure accuracy and reliability. If the product passes all tests, it moves to the next stage, which involves an audit of the manufacturing facility. This audit ensures that the production process aligns with the standards and that quality control measures are consistently applied.
Upon successful completion of the testing and audit phases, the product is awarded SNI certification. This certification is valid for a specific period, typically three years, after which it must be renewed. During this period, the certification body may conduct periodic inspections to ensure ongoing compliance. Businesses that achieve SNI certification can display the SNI logo on their products, signaling to consumers that the product meets national quality benchmarks. This certification not only enhances market credibility but also provides a competitive edge in both domestic and international markets.
Steps in the SNI Certification Process
- Submit an application with detailed product information
- Undergo product testing by accredited laboratories
- Facility audit to verify compliance with production standards
- Receive certification upon successful evaluation
- Periodic inspections to ensure ongoing compliance
Key Sectors Impacted by SNI
SNI standards have a profound impact on various sectors, ensuring that products and services meet stringent quality and safety benchmarks. One of the most significantly affected sectors is the food and beverage industry. SNI standards in this sector cover everything from food safety and hygiene to nutritional labeling and packaging requirements. For example, SNI mandates that food products undergo microbial testing to ensure they are free from harmful bacteria, thereby safeguarding public health.
The construction and building materials sector is another area where SNI plays a critical role. SNI standards for construction materials, such as cement, steel, and bricks, ensure that these products meet specific strength, durability, and safety criteria. This is particularly important in a country like Indonesia, where natural disasters like earthquakes and floods are common. By adhering to SNI standards, construction companies can build structures that are not only aesthetically pleasing but also resilient to environmental challenges.
The electronics and electrical appliances sector is also heavily influenced by SNI. Products such as refrigerators, air conditioners, and smartphones must comply with SNI standards related to energy efficiency, electrical safety, and environmental impact. For instance, SNI mandates that electrical appliances undergo safety tests to prevent hazards like overheating or electrical fires. This ensures that consumers receive products that are not only functional but also safe to use, thereby enhancing consumer confidence and market competitiveness.
SNI Standards in Key Sectors
Sector | SNI Standards | Impact |
---|---|---|
Food and Beverage | Food safety, hygiene, nutritional labeling | Ensures safe and healthy food products |
Construction | Material strength, durability, safety | Builds resilient and safe structures |
Electronics | Energy efficiency, electrical safety | Ensures safe and efficient appliances |
Challenges in SNI Implementation
While SNI standards offer numerous benefits, their implementation is not without challenges. One of the primary obstacles is the cost associated with obtaining and maintaining SNI certification. For small and medium-sized enterprises (SMEs), the expenses related to product testing, facility audits, and ongoing compliance can be prohibitive. This financial burden often discourages smaller businesses from pursuing SNI certification, limiting their ability to compete in the market.
Another significant challenge is the lack of awareness and understanding of SNI standards among businesses and consumers. Many companies, especially those in rural or less-developed areas, are unaware of the importance of SNI certification or the process involved. Similarly, consumers may not fully understand the significance of the SNI logo, leading to a lack of demand for certified products. This gap in knowledge can hinder the widespread adoption of SNI standards and undermine their effectiveness.
Additionally, the enforcement of SNI standards can be inconsistent, particularly in industries where regulatory oversight is weak. While some sectors, such as food and electronics, have stringent enforcement mechanisms, others may face challenges due to limited resources or corruption. This inconsistency can create an uneven playing field, where compliant businesses are at a disadvantage compared to those that bypass the certification process. Addressing these challenges requires a concerted effort from the government, industry stakeholders, and consumers to promote awareness, provide financial support, and strengthen enforcement mechanisms.
SNI vs International Standards
Comparing SNI standards with international benchmarks, such as those set by the International Organization for Standardization (ISO), reveals both similarities and differences. SNI standards are often aligned with ISO guidelines to ensure compatibility and facilitate international trade. For example, SNI's standards for environmental management systems closely mirror ISO 14001, promoting sustainable practices across industries. This alignment helps Indonesian businesses meet global requirements and access international markets more easily.
However, there are also distinctions between SNI and international standards. SNI standards are tailored to address specific local conditions and priorities, such as Indonesia's unique climate, cultural practices, and economic needs. For instance, SNI standards for construction materials take into account the country's susceptibility to earthquakes and tropical weather, which may not be a focus in international standards. This localization ensures that SNI standards are practical and relevant for domestic businesses and consumers.
Despite these differences, the collaboration between SNI and international organizations continues to grow. Indonesia actively participates in global standardization forums, contributing its expertise and adopting best practices from other countries. This collaboration not only enhances the credibility of SNI standards but also positions Indonesia as a key player in the global standardization landscape. By balancing local needs with international benchmarks, SNI ensures that its standards remain robust, relevant, and globally competitive.
Comparison Table: SNI vs ISO Standards
Aspect | SNI Standards | ISO Standards |
---|---|---|
Focus | Local conditions and priorities | Global best practices |
Adaptability | Tailored to Indonesia's unique needs | Universal application |
Collaboration | Aligned with ISO for international |
- Alex Lopez Meet Diana Zubiris Loving Husband
- A Mothers Unwavering Embrace Chapter Three Jackermans Heartfelt Journey
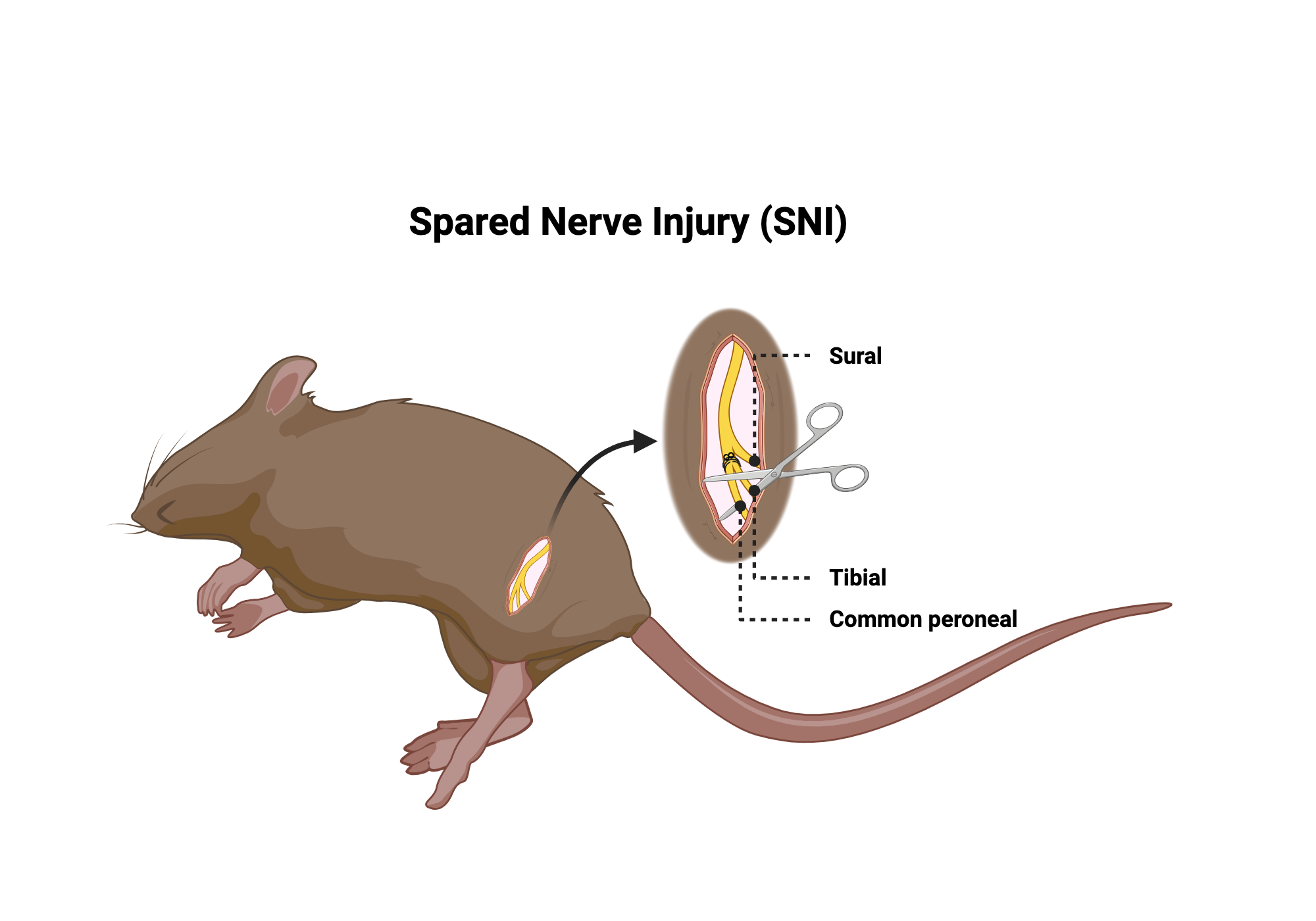
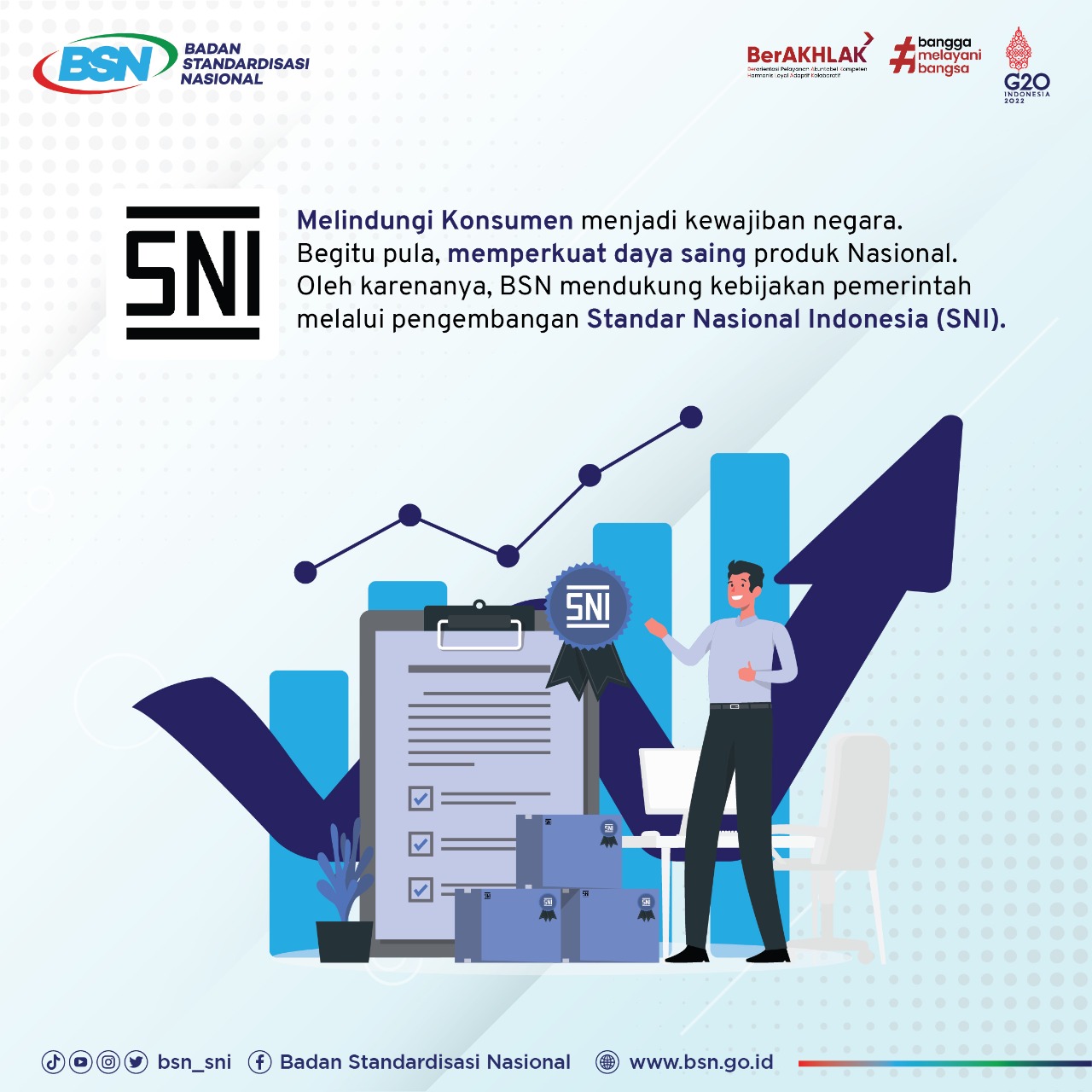